How 3D LiDAR Scanning Adds Value for Industrial & Manufacturing Clients
In the following, Clark Nexsen’s James Meadows, PE, presents the benefits of using 3D LiDAR scanning in industrial and manufacturing settings to accelerate engineering projects:
w
According to manufacturing firms like http://www.picomes.com/, time is money in the manufacturing world. Industrial mechanical engineering upgrades need to be executed in the shortest possible window – but these upgrades are often being made in plants with complex existing systems, and no single source of accurate documentation. LiDAR scanning (Light Detection and Ranging) offers critical benefits to clients and engineers, translating rapidly to 3D models that make projects more efficient and minimize conflicts in the field.
It Saves Time & Brings Projects Online More Rapidly
Often, industrial and manufacturing clients don’t have thorough existing documentation of their plant. LiDAR scans can be used to quickly and accurately document the existing conditions of a plant – typically taking two to three days to complete compared to weeks when using traditional surveying. The scans are accurate to 1/8th of an inch, which is more reliable than traditional surveying.
3D LiDAR scanning makes it possible for our team to measure anything in the files – pipe diameters, structure diameters, distances, etc. This is invaluable in the design process for new systems.
The Clark Nexsen industrial team takes the 3D scan and creates a full 3D model, general arrangements, and elevation drawings. With these tools, we have every piece of data we need to design the new system without having to go on site every few days to verify where things are located. It all comes down to better accuracy and less time, making the design and construction process faster.
The Upfront Investment Delivers Future Cost Savings
In addition to reducing costs for a team to complete traditional surveying, 3D scanning pays for itself by making future design projects less expensive, faster, and easier to coordinate. It offers a more comprehensive view of whatever area of the plant is scanned, allowing future projects to take place without additional scanning and minimal field verification. As new systems are designed within the model and drawing files, the documentation remains current and accurate for long-term use.
It Minimizes Conflicts in the Field
When it comes to construction, avoiding conflicts in the field that result in change orders and delays is critical. The accuracy of the scans in documenting existing conditions is instrumental in this effort. I have been part of multiple projects now where I’ve modeled new additions and then evaluated them in the scan to identify coordination issues. The ability to transpose new designs into the existing plant conditions defined by the scan allows us to avoid generating designs that conflict with the existing operations. Finding conflicts in design reduces the likelihood of a future change order for the client.
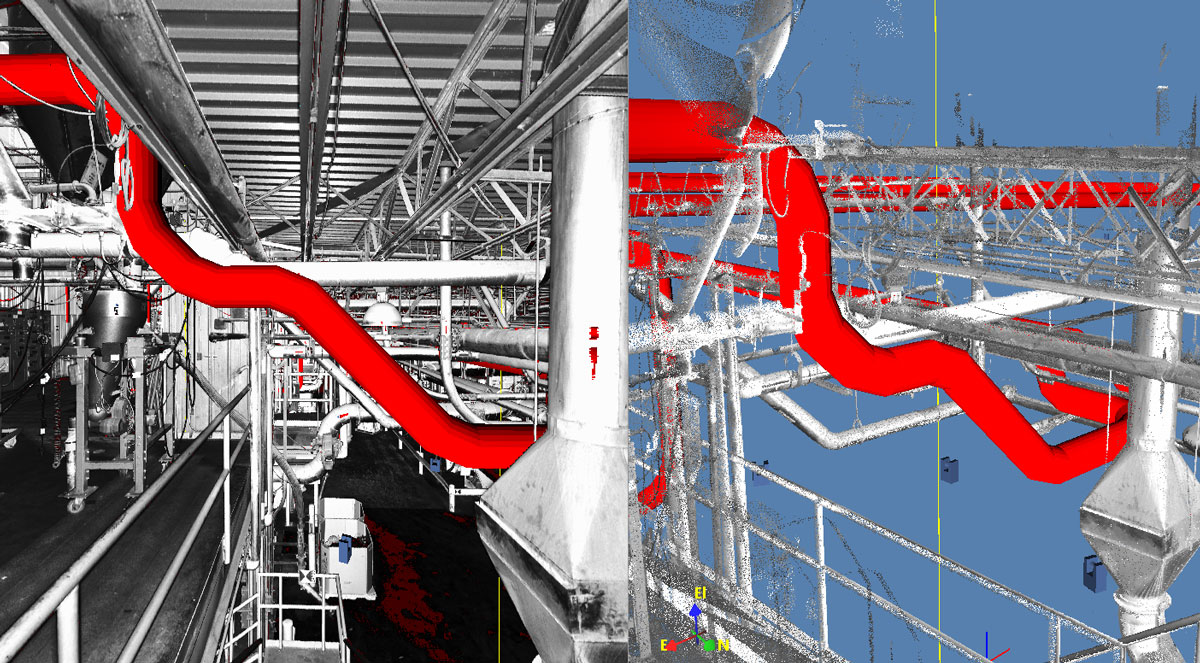
One of the reasons this technology is so well-suited to supporting industrial and manufacturing clients is that in a plant setting, everything the scanner needs to see is there to be seen – systems aren’t hidden behind walls or in ceilings in the same way as other building types.
3D LiDAR scanning makes it possible for our team to measure anything in the files – pipe diameters, structure diameters, distances, etc. This is invaluable in the design process for new systems.
Without getting too granular, the scanning technology works by using light waves from a laser and calculating how long it takes for the light to hit an object or surface and reflect back to the scanner. Distances are then calculated using the velocity of light. Depending on the sensor used, LiDAR can fire hundreds of thousands of pulses per second, and each of these measurements can be processed into a 3D visualization known as a ‘point cloud.’ Personally, I have been part of 10 projects in which we used 3D scanning, and I see its use only growing as clients realize its benefits.
James Meadows, PE, is an industrial mechanical engineer in our Macon, GA office. As a project manager, he has taken an active role in the conceptualization and execution of many projects including industrial minerals, pulp and paper, bio-fuels, plastics, and facility improvements. To learn more about 3D scanning applications for manufacturing settings or to speak with James, please call 478.743.8415 or email jmeadows@clarknexsen.com.